Caoutchoucs synthétiques à usage général
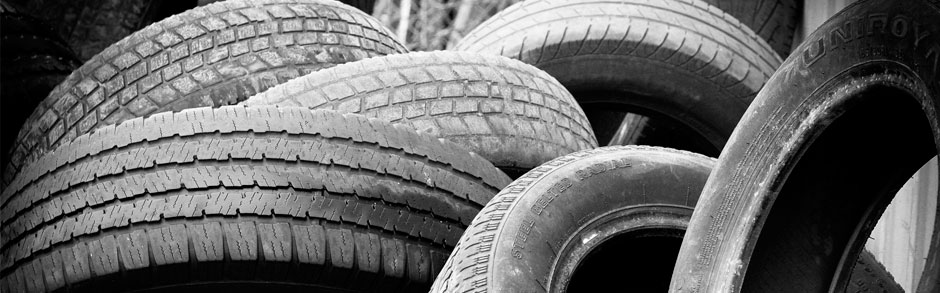
Les caoutchoucs synthétiques sont normalement utilisés dans les applications où certaines caractéristiques clés telles qu'une forte abrasion ou une faible perméabilité sont nécessaires.
Grâce à l’IR, on est parvenu à obtenir par synthèse un matériau équivalent au caoutchouc naturel et sa formulation est semblable à celui-ci. Lors des opérations de moulage, par compression comme par injection, ces polyisoprènes synthétiques s’écoulent plus facilement que le caoutchouc naturel, ce qui peut s’avérer notamment avantageux concernant le moulage par injection, ou la fabrication de pièces compliquées ou de faible épaisseur et grande surface ; par contre, sa moindre résistance à la déchirure, surtout aux températures de vulcanisation, peut provoquer des difficultés lors du démoulage de ces pièces compliquées.
Lors de l’extrusion, le calandrage et la confection d’articles composites, les polyisoprènes synthétiques ne présentent aucune difficulté spéciale, sauf celles pouvant provenir de sa moindre ténacité et résistance à cru et, dans le cas de ceux obtenus avec le butyl-lithium, de son écoulement à froid. La moindre tendance à la cristallisation que possèdent les polyisoprènes synthétiques se traduit par des valeurs plus basses de dureté, rigidité, résistance à la traction et à la déchirure, ainsi que par un moindre taux de rétention de ces mélanges sans charge.
La plus grande pureté des polyisoprènes synthétiques entraîne une meilleure performance comme isolant électrique, ainsi qu’une moindre coloration. Étant donné qu’il s’agit de matériaux synthétiques, ils présentent une uniformité de caractéristiques impossibles pour le caoutchouc naturel.
Caoutchoucs de Butadiène-Styrène (SBR)
Les caoutchoucs de butadiène-styrène constituent le type de caoutchouc synthétique le plus consommé. Tout comme le caoutchouc naturel, le SBR peut vulcaniser par le soufre et les accélérateurs, au moyen de peroxydes ou au moyen d’autres agents vulcanisants spéciaux.
Le SBR est moins sensible à la rouille que le caoutchouc naturel, de par sa nature même et parce qu’il est pourvu d’un antirouille. En outre, les SBR exigent la présence de charges renforçantes pour atteindre un niveau satisfaisant de résistance mécanique. Avec de telles charges, on obtient une résistance à l’abrasion qui dépasse souvent celle du caoutchouc naturel.
Les caoutchoucs SBR sont nettement inférieurs au caoutchouc naturel en ce qui concerne la résilience. Quant à la tenue à la fatigue dynamique, les SBR sont meilleurs que le caoutchouc naturel concernant leur retard dans l’apparition des fissures, mais dès que celles-ci se manifestent, par fatigue ou dues à une éventuelle lacération mécanique, elles se propagent plus vite que dans les caoutchoucs naturels vulcanisés.
Quant à ses principales applications, il faut souligner la fabrication d’enveloppes de pneus, isolement de câbles, articles techniques moulés, chaussures, courroies, tuyaux, ou adhésifs, entre autres.
Caoutchoucs de Polybutadiène (BR)
Les polymères de butadiène figurent parmi les premiers caoutchoucs synthétiques fabriqués à échelle industrielle. Lorsqu’ ils sont les seuls caoutchoucs à être utilisés lors d’une vulcanisation, les BR à haute teneur en cis-1,4 donnent un taux plus élevé de résistance à la traction et à la déchirure, ainsi que d’allongement de rupture.
Sa résistance à l’abrasion est également meilleure, celle de tous les BR étant supérieure à celles du SBR et du caoutchouc naturel.
L’une des particularités des produits vulcanisés de BR est leur résilience élevée, celle-ci étant, à température ambiante, même supérieure à celle du caoutchouc naturel. Sa résistance au froid est également excellente. Les BR à haute teneur en cis conservent leur haute résilience à des températures aussi basses que -40ºC.
Si lors d’une formulation à base de caoutchouc naturel on remplace progressivement celui-ci par le BR, jusqu’à ce que la proportion de ce dernier ne dépasse une valeur d’environ 40-45 pour cent, aucun empirement visible ne se produira concernant les caractéristiques d’élaboration, obtenant, par contre, les avantages suivants:
- Une meilleure résistance à l’abrasion
- Une moindre tendance aux fissures par fatigue
- Une plus grande résistance à la réversion
D’une façon analogue, dans le cas d’une formulation à base de SBR, tant que le remplacement de celui-ci par BR n’a pas atteint une valeur d’environ 50% de celui-la, les caractéristiques d’élaboration ne sont pas affectées d’une façon perceptible, obtenant, par contre:
- Une meilleure résistance à l’abrasion
- Une moindre tendance aux fissures par fatigue
- Une résilience plus élevée et une moindre hystérésis, ce qui se traduit par une moindre génération de chaleur et, par conséquent, de moindres températures de rodage
Autres matériels
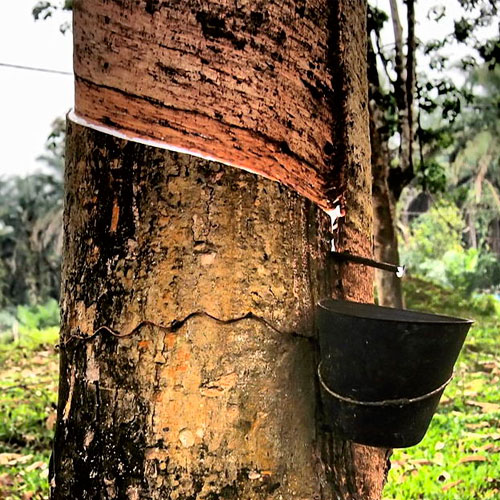
Caoutchouc naturel (NR)
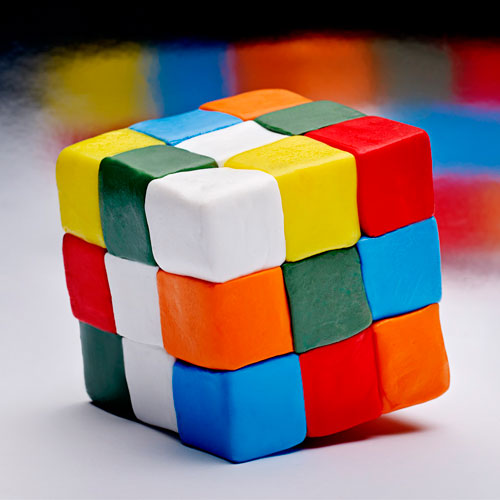