Synthesekautschuk für den Allgemeingebrauch
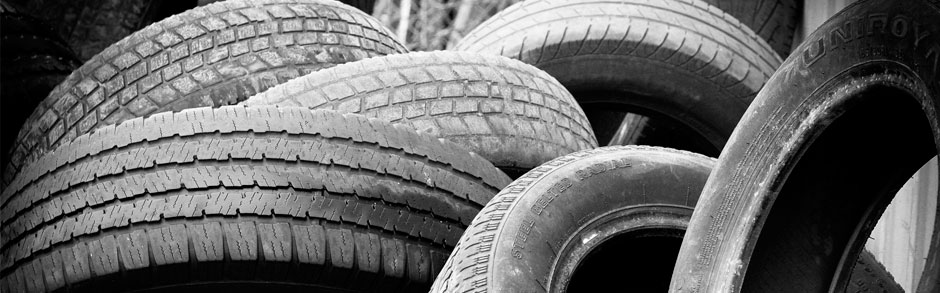
Synthesekautschuk wird üblicherweise für Anwendungen verwendet, für die hohe Abrasion oder niedrige Permeabilität erforderlich sind.
Synthetische Polyisoprene (IR)
Dank IR war es möglich, ein dem Naturkautschuk äquivalentes Material zu erhalten und auch die Ausfertigung ist dem Naturkautschuk ähnlich. Beim Formpressen und Spritzgießen fließen diese synthetischen Polyisoprene wesentlich leichter als Naturkautschuk, was besonders beim Spritzgießen oder der Herstellung von komplexen oder dünnen und großen Teilen von Vorteil ist; doch die niedrige Reißfestigkeit, vor allem bei den Temperaturen der Vulkanisation, kann bei solch komplexen Teilen zu Schwierigkeiten bei dem Entnehmen aus der Form führen.
Bei der Extrusion, Kalandrierung und Anfertigung von Verbundartikeln präsentieren die synthetischen Polyisoprene keine speziellen Schwierigkeiten, mit Ausnahme derer, die sich aus der verringerten Festigkeit und Widerstandskraft des unverarbeiteten Materials ergeben können sowie bei denen, die mit kalt fließendem Lithium erhalten wurden. Synthetische Polyisoprene weisen eine schwächere Kristallisierungstendenz auf, was sich in niedrigeren Werte von Härte, Steifigkeit, Reiß- und Zugfestigkeit sowie in einer reduzierten Retentionsrate dieser Mischungen ohne Lasten zeigt.
Die höhere Reinheit der synthetischen Polyisoprene bietet eine bessere Leistung als elektrischer Isolator. Da es sich um synthetische Materialien handelt, weisen sie homogene Eigenschaften auf, die Naturkautschuk nicht erzielen kann.
Styrol-Butadien-Kautschuk (SBR)
Styrol-Butadien-Kautschuk ist der am meisten gebrauchte Synthesekautschuk. Ebenso wie Naturkautschuk kann SBR mit Schwefel und Beschleunigern vulkanisiert werden, durch Peroxide oder andere spezielle Vulkanisationsagenten.
SBR ist weniger anfällig für die Oxidation als Naturkautschuk, teils weil er bereits ein Antioxidans enthält, teils aufgrund seiner intrinsischen Eigenschaft. Außerdem benötigen die SBR verstärkende Ladungen, um eine zufriedenstellende mechanische Beständigkeit zu erzielen. Mit diesen Ladungen wird eine Abrasionsbeständigkeit erzielt, die oft die des Naturkautschuks übertrifft.
SBR-Kautschuk weist eine wesentlich niedrigere Belastbarkeit als Naturkautschuk auf. Bezüglich der dynamischen Belastung ist SBR besser als Naturkautschuk, da erst später Risse auftreten, doch sind diese einmal vorhanden, sei es durch Belastung oder durch eventuelle mechanische Risse, breiten sie sich schneller aus als bei vulkanisiertem Naturkautschuk.
Die hauptsächlichen Verwendungszwecke umfassen unter anderem Reifen, Kabelisolierung, geformte technische Artikel, Schuhe, Gürtel, Schläuche oder Klebstoffe.
Polybutadien-Kautschuk zählt zu den häufigsten industriell hergestellten Synthesegummis. Wenn er bei einer Vulkanisation als einziger Kautschuk verwendet wird, ergeben die BR mit hohem cis-1,4 höhere Beständigkeitswerte bezüglich Reiß-, Zug- und Verlängerungsfestigkeit.
Ihre Abrasionsstärke ist ebenfalls besser, welche bei allen BR höher als bei SBR und Naturkautschuk ist.
Einer der Haupteigenschaften von BR ist die Widerstandsfähigkeit der vulkanisierten Produkte, die wesentlich höher als die von Naturkautschuk bei Zimmertemperatur ist. Die Kältebeständigkeit ist ebenfalls herausragend. BR mit hohem cis-Wert kann Temperaturen bis zu -40ºC aushalten.
Wenn Naturkautschuk progressiv durch BR in einer Verbindung ersetzt wird, bis das Verhältnis dieser einen Wert von circa 40-45 Prozent nicht überschreitet, wird keine Verschlechterung der Produktionseigenschaften, aber die folgenden Vorteile erzielt:
- Bessere Abrasionsbeständigkeit
- Verringerte Tendenz zu Rissen durch Belastung
- Höhere Reversionsbeständigkeit
Im Fall von SBR-Verbindungen erzielen wir die folgenden Vorteile, wenn bis zu 50 % durch BR ersetzt wird:
- Bessere Abrasionsbeständigkeit
- Verringerte Tendenz zu Rissen durch Belastung
- Höhere Belastbarkeit und niedrigere Hysterese, was eine niedrigere Wärmeerzeugung und daher niedrigere Betriebstemperaturen bedeutet
Andere Materialien
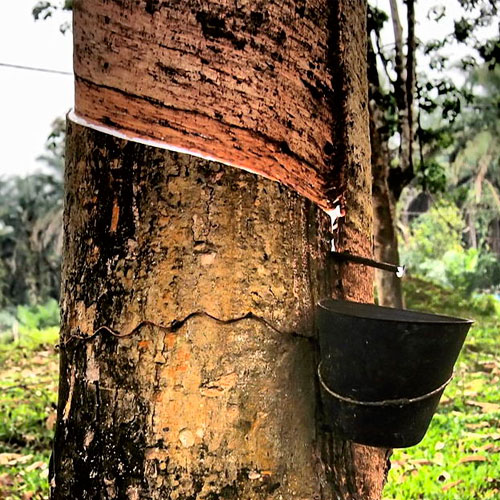
Naturkautschuk
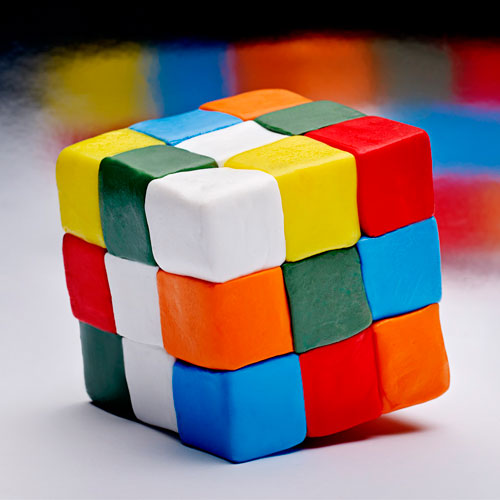