Laboratory
COECA has developed a philosophy focused on satisfying our customers' needs and expectations. Continual progression for us is fundamental to meet our objectives, adapting ourselves to the present market demands. That’s why COECA invests huge efforts towards the research and development of new materials and new production processes.
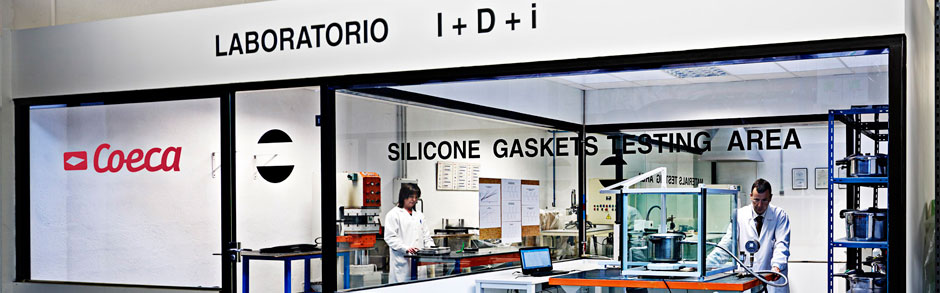
COECA has its own laboratory, which lets us deal with and give a solution to the strictest requirements, as well as to carry out a rigorous quality control of our materials.
Our laboratory lets us test and control all our production processes: compounds preparation, physical-chemical properties tests of our materials, and finished part dimensional control.
We use cutting-edge equipment such as:
- Compact OD PC Rheometer: used to test the vulcanisation process
- Mooney Compact PC Viscometer: used for viscosity tests
- PC Dynamometer: used for tensile strength, elongation at break and tear strength tests
- PC Electronic Densimeter: used for density tests
- PC-Micro-IRHD Automatic Durometer: used to measure hardness in a Micro-IRHD scale
- PC-IRHD Automatic Durometer: used to measure hardness in a IRHD scale
- PC-SHORE Automatic Durometer: used to measure hardness in a SHORE A scale
- Low Temperature Equipment: used for low temperature tests
- MEMMERT 500 Stove: used for ageing, compression set and swelling into fluids strength tests
- Multi-die cut: with adjustable accessories to get standard test tubes
- Laboratory Injection Machine: 50 tonnes shutting strength
- Laboratory Press: 250 atm. maximum working press
- Laboratory Cylinder: used to prepare and approve new compounds
All tests are carried out under normalised conditions according to each norm. BS, DIN, ASTM y UNE are the most usual norms used in our laboratory.
We also have a laboratory specially designed to test pressure cooker silicone gaskets. We have developed all necessary equipment to guarantee the proper working of our pressure cookers silicone seals. We carry out research and development projects together with our customers to continually improve the performance of our silicone seals for our customers’ pressure cookers.
We have developed a measuring instrument for the necessary torque setting to open and close the cooker. We are developing a project with the aim to reduce the friction degree of the silicone seal into the lid until it reaches similar values to the silicone seals performance after common industrial surface treatments are applied.
Moreover, we have designed an automatic measuring instrument for the pressure relieving point of the pressure cooker. The pressure relieving point is the maximum pressure the silicone seal can support into the cooker before it performs the inside water-steam extraction. This is a key instrument to guarantee the pressure cooker safety.